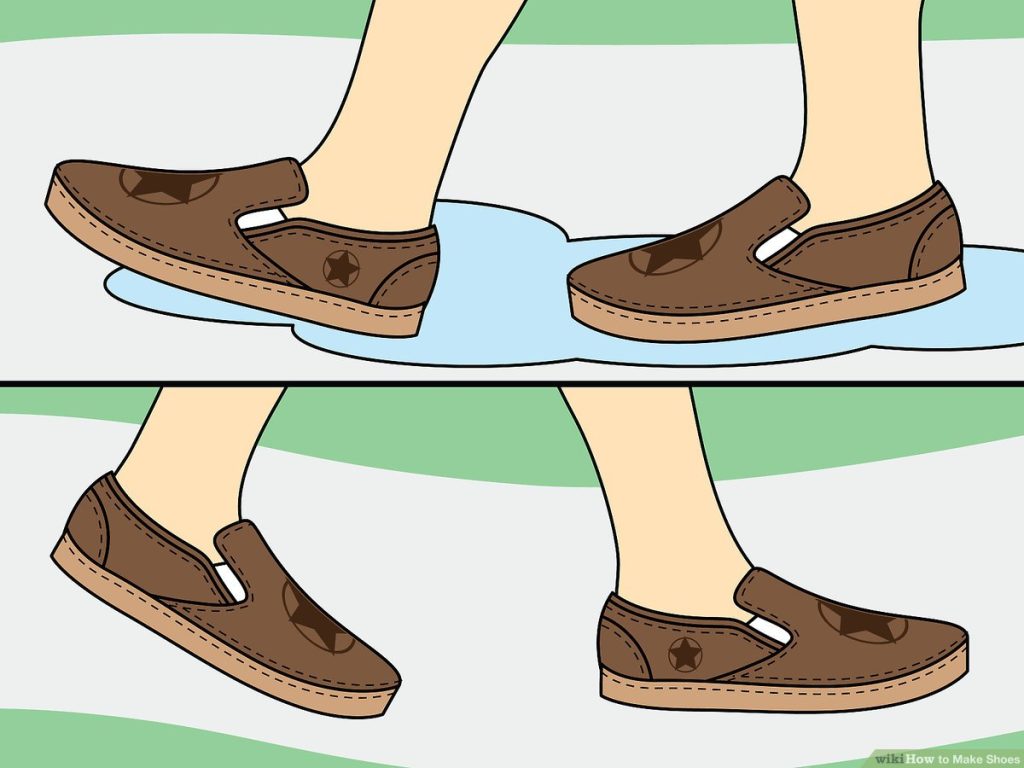
Shoes make fashion important. After all, you hang out in it all day, so why not wear shoes and pizza? While it can be a bit of a chore in untrained hands, it’s entirely possible to make your own pair of shoes at home. To make shoes you need to gather the right materials, make a cast of the foot, cut the shoe parts to size, assemble the parts and finalize the design. Once you’ve mastered the basics, you don’t have to depend on store brands for your look. Few things can look as cool as a unique set of shoes, and they can be really fun to make once you get the hang of how it works
Preparation of materials
Decide what kind of shoe you want to make
If you’re going to make a shoe, it’s undoubtedly important that you have an idea of what kind of shoe you want to make. Shoes are incredibly versatile, and you can make many different types, including but not limited to loafers, sneakers, sandals, boots, and heels. Try to imagine which shoe model best suits your personal style.
- It may be helpful to list a few ideas. Expressing ideas with images can go a long way in designing a shoe.
- If you’re new to shoemaking, it’s probably best to stick with something simple. A standard lace-up will do without the finesse of fancier types and you can still add a lot of style to the basic formula.
Draw, find or buy a design for your shoes
Before thinking about making a shoe, it is important to have accurate and detailed work plans. After all, you don’t want to make design decisions on the go; shoemaking is a very precise business and even the smallest mishap can prevent the success of a shoe.
Basic shoe designs can be found on the Internet. Do a search and find some “recipes”. If nothing else, it can provide inspiration for your design.
- Online art stores like www.etsy.com may have more detailed shoe designs for sale.
- Creating your own design is only recommended if you’ve already made a shoe. If that’s what you ultimately want to do, try sewing some basics with a free pattern and use that experience to create your own next time.
Collect parts of an old shoe
You can save a lot of time and give your shoes a more professional look if you collect parts from other unused shoes. Shoe soles are especially good because they give you a reference for the rest of your sewing. Provided they’re in good shape, salvage the parts you think might work in your new shoes and slowly and carefully remove them with the blade of a scalpel.
Get the rest of the materials from a hardware store or specialty store
While specific ingredient lists depend on the specific type of shoe you want to make, it usually goes without saying that you need a few sheets of good leather and sturdy fabric.
- If you don’t have a sewing and sewing kit, you’ll need to buy or borrow one to make your shoes.
- Rubber, leather, and textiles are all good for the body of shoes.
- Although it is recommended to take shoe soles from old shoes or buy them ready-made as accessories, it is possible to create a functional and waterproof sole with some cork boards. Each sheet should be no more than 1/8 inch thick.
- Make sure you get at least double what you think so you have enough for a couple!
Making a foot cast
Create a custom duration
The last is a block shaped like a human foot that cobblers use to guide their work. You can do this by making a plaster cast of your foot; The shoes you make this way are custom made just for you. Take a box full of alginate jelly and put your feet in it, preferably up to your ankles. Let your feet sit for 20 minutes while the jelly hardens, then slowly remove them.
- Remember to slowly remove your feet; you don’t want to damage anything when setting up.
- It is highly recommended to do this on both legs at the same time. Downtime is best overcome early in the process.
- One good thing to mention at this stage of the process is that you can ideally reuse these lasts on any subsequent pair of shoes you attempt to make.
Pour the casting material into your casting box
Now that you have a good mold for your leg, you can pour some casting material into it. Depending on the type and quality of the casting material, the solidification time can vary from half an hour to overnight. Be patient: At this point it might be a good time to work on other parts of the process if your plans are clear enough.
Remove and secure the last one
When the latter has hardened, it’s time to take it out and cook. Cover the latter with colorless tape. This way it is less likely to get damaged and you can draw your design directly on it.
Draw your design to the last. Before you start putting the pieces together, it’s probably helpful to give the latter an outline of how you want the shoe to look around it. While you shouldn’t rely on it for actual measurements, an idea of what it looks like in three dimensions will help you figure out where each stitch should go.